Fiberglass mesh has emerged as a high-performance construction material widely used in waterproofing engineering in recent years. This article comprehensively examines the unique value of fiberglass mesh in waterproofing applications by analyzing its material properties, waterproofing mechanisms, construction techniques, application scenarios, and future development trends. Through an evaluation of key performance indicators such as tensile strength, corrosion resistance, and dimensional stability, the article highlights its irreplaceable role in roofing waterproofing, basement waterproofing, and bridge and tunnel projects. Additionally, it details composite application technologies combining fiberglass mesh with other waterproofing materials and critical quality control points during construction, providing practical guidance for engineering professionals.
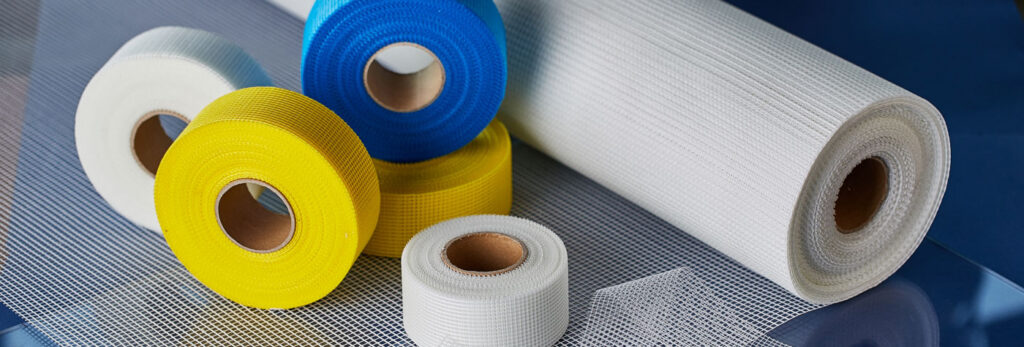
Overview and Waterproofing Mechanism of Fiberglass Mesh
Fiberglass mesh is a new construction material made from medium- or alkali-free glass fiber yarns, processed through specialized weaving techniques and coated with alkali-resistant polymer emulsions. This mesh features a unique grid structure, with mesh sizes typically ranging from 3mm×3mm to 10mm×10mm and weights varying between 80g/m² and 300g/m², customizable to project requirements. In waterproofing applications, fiberglass mesh primarily serves as reinforcement, crack resistance, and stress distribution, making it an indispensable component in modern waterproofing systems.
From a material composition perspective, high-quality fiberglass mesh incorporates 16.7% zirconium oxide (ZrO₂) in the glass fibers. The raw materials are melted at 1600°C, and during fiber formation, the filaments are coated with water-soluble epoxy resin and coupling agents. This specialized treatment grants the mesh exceptional alkali resistance, enabling it to withstand corrosive alkaline substances like Ca(OH)₂ in cement mortar. Additionally, the mesh is further coated with a highly alkali-resistant synthetic polymer, forming a tough, durable protective layer that enhances long-term performance.
The waterproofing mechanism of fiberglass mesh is based on three key functions: mechanical reinforcement, stress distribution, and crack prevention. When combined with asphalt, polymer-modified asphalt, or other waterproofing membranes, the high-strength fiber skeleton of the mesh significantly improves the tensile and tear resistance of the waterproofing layer. Experimental data show that premium fiberglass mesh can achieve tensile strengths of 1,200–3,000 N/50mm in both warp and weft directions, with an elastic modulus of up to 80.4 GPa. This high strength enables the material to effectively counteract deformation stresses caused by temperature fluctuations, wind loads, or foundation settlement.
The waterproofing performance of fiberglass mesh also benefits from its excellent chemical stability. The material is resistant to alkalis, acids, water, and cement erosion, ensuring long-term stability without degradation. According to China’s JG158-2004 standard, high-quality fiberglass mesh must retain at least 90% of its tensile strength after alkali exposure, guaranteeing reliability in alkaline environments. This chemical stability makes fiberglass mesh particularly suitable for waterproofing concrete structures, where continuous alkaline emissions can corrode conventional fiber materials.
Table: Key Performance Indicators of Fiberglass Mesh
Performance Indicator | Typical Value | Test Standard | Significance in Waterproofing |
---|---|---|---|
Warp Tensile Strength | 1,200–3,000 N/50mm | JG158-2004 | Enhances tensile resistance |
Weft Tensile Strength | 1,200–3,000 N/50mm | JG158-2004 | Improves multi-directional stress resistance |
Alkali Resistance Retention | ≥90% | JG158-2004 | Ensures long-term durability |
Elongation at Break | ≤2.4% | – | Reduces cracking risk |
Weight per Unit Area | 80–300 g/m² | – | Balances strength and workability |
In waterproofing applications, fiberglass mesh is typically used with asphalt-based membranes, polymer-modified asphalt coatings, or polyurethane waterproofing materials. When waterproofing media (e.g., asphalt) lack sufficient strength, external forces such as temperature changes and UV exposure can lead to cracking and leaks. However, waterproofing systems reinforced with fiberglass mesh significantly improve weather resistance and tensile strength, enabling the waterproofing layer to withstand stress variations without cracking. This “flexible yet rigid” composite waterproofing concept has become a mainstream approach in modern construction waterproofing.
Primary Applications of Fiberglass Mesh in Waterproofing Engineering
Thanks to its outstanding physical properties and chemical stability, fiberglass mesh offers broad application potential in building waterproofing. From roofing to underground structures, bridges, tunnels, and interior damp-proofing, this material plays a crucial role. Understanding these application scenarios and their technical requirements helps engineers select and install fiberglass mesh more effectively, ensuring waterproofing quality and longevity.
Roofing waterproofing systems are one of the most common applications for fiberglass mesh. Traditional asphalt roofing membranes are prone to cracking and leaks due to temperature fluctuations and UV exposure. However, when reinforced with fiberglass mesh, the waterproofing layer’s overall performance improves significantly. In practice, fiberglass mesh is often combined with polymer-modified asphalt membranes to form “one-layer, one-coat” or “multi-layer, multi-coat” waterproofing structures. The mesh acts as “soft rebar,” evenly distributing thermal stresses and preventing concentrated cracking. For steep-slope roofs, the reinforcing effect is even more pronounced, preventing membrane slippage or flow under high temperatures. Research by Saint-Gobain shows that roofing systems reinforced with fiberglass mesh can extend service life by over 50% compared to traditional methods.
Basement waterproofing demands materials with high water pressure resistance and impermeability, where fiberglass mesh excels. In basement walls and exterior waterproofing, the mesh is typically paired with polymer-modified cementitious coatings. The construction process involves applying a base coat of waterproofing slurry, embedding the fiberglass mesh, rolling out air bubbles, and finishing with a topcoat. This “sandwich” structure creates a waterproofing layer that resists seepage while accommodating minor cracks and substrate movements. Given the damp and highly alkaline basement environment, the mesh’s alkali resistance is critical. Test data show that premium alkali-resistant fiberglass mesh retains over 95% of its strength after 28 days in saturated Ca(OH)₂ solution, meeting long-term waterproofing requirements.
In exterior insulation finishing systems (EIFS), fiberglass mesh is vital for crack resistance and waterproofing in the protective layer. Modern buildings widely use external insulation, but the outer mortar layer is prone to cracking, allowing water infiltration. Embedding fiberglass mesh in the mortar significantly enhances crack resistance and waterproofing. During installation, a base coat of anti-crack mortar is applied, followed by fiberglass mesh (with ≥100mm overlaps), and finally a finish coat (3–5mm total thickness). This assembly prevents cracking while distributing stresses across the wall system. For EIFS applications, fiberglass mesh with 4×4mm or 5×5mm grids and a weight ≥160 g/m² is recommended to ensure sufficient mechanical performance.
Bridge and tunnel waterproofing imposes even stricter material requirements, where fiberglass mesh is increasingly used. In concrete bridge deck waterproofing, a composite system of fiberglass mesh and high-elasticity modified asphalt coatings accommodates dynamic loads, preventing fatigue failure. For underground structures like subway tunnels, fiberglass mesh-reinforced waterproofing must withstand high water pressure, alkaline concrete conditions, and structural movements. Case studies by Nantong Top New Materials show that specialized fiberglass mesh (e.g., ARNP6×6-100L, 300 g/m²) delivers excellent stability and durability in complex geological conditions.
Table: Application Characteristics of Fiberglass Mesh in Different Waterproofing Projects
Application | Common Specifications | Compatible Materials | Key Technical Points |
---|---|---|---|
Roofing | 5×5mm, 160–300 g/m² | Modified asphalt membranes/coatings | Thermal movement resistance, UV stability |
Basements | 4×4mm or 5×5mm, ≥160 g/m² | Polymer-modified cementitious coatings | Water pressure resistance, alkali resistance |
EIFS | 4×4mm or 5×5mm, 160 g/m² | Anti-crack mortar | Crack resistance, stress distribution |
Bridges/Tunnels | 6×6mm or larger, ≥300 g/m² | High-elasticity modified asphalt | Dynamic load resistance, high water pressure resistance |
Additionally, fiberglass mesh is widely used in interior damp-proofing, water tank waterproofing, and underground utility tunnel waterproofing. In bathrooms and kitchens, lightweight mesh (80–125 g/m²) with waterproof coatings provides moisture protection without adding thickness. For large water tanks and sewage treatment facilities, corrosion-resistant fiberglass mesh paired with chemically stable materials (e.g., epoxy resins) ensures long-term waterproofing performance.
As construction technology evolves, fiberglass mesh applications continue to innovate. Examples include self-adhesive prefabricated membranes for easier installation, integrated mesh-coating systems for efficiency, and specially treated meshes for enhanced bonding. These advancements further expand fiberglass mesh’s role in waterproofing, solidifying its status as a cornerstone of modern waterproofing systems.