Chemical fiber mesh felt, a non-woven fabric made from synthetic fibers, boasts a wide array of applications due to its unique material properties. Its versatility stems from the ability to tailor its characteristics through fiber type selection, fiber diameter, density, and finishing processes.
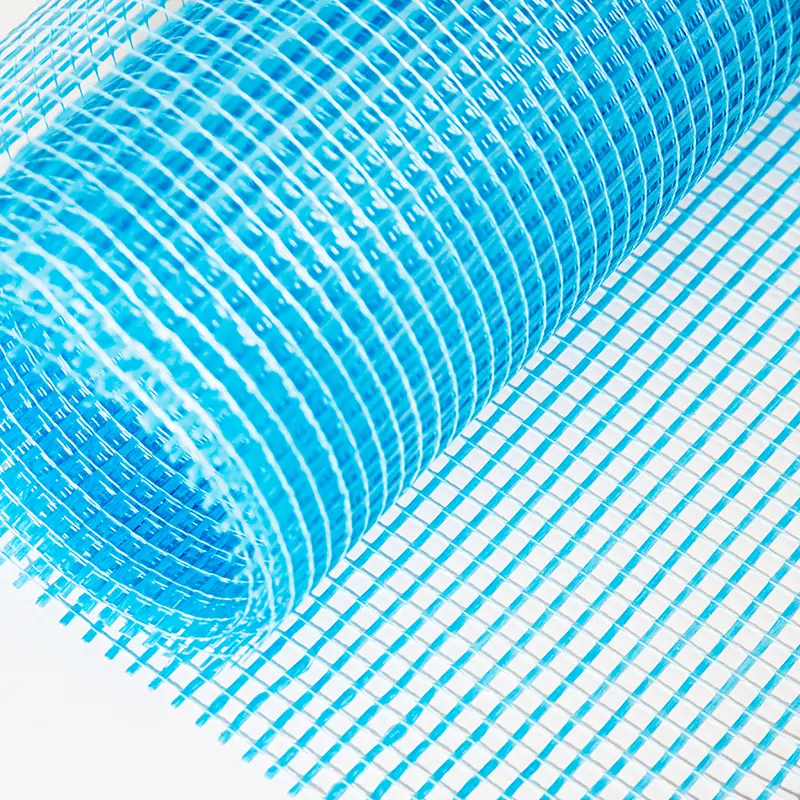
Material Properties:
- Fiber Type: The choice of fiber significantly impacts the felt’s properties. Common fibers include polyester, polypropylene, nylon, and acrylic. Polyester offers excellent tensile strength and chemical resistance, making it suitable for demanding applications. Polypropylene provides lightweight and cost-effective solutions, while nylon excels in abrasion resistance. Acrylic fibers can offer specific properties like flame retardancy.
- Fiber Diameter: Finer fibers lead to a smoother, denser felt with improved filtration capabilities and a softer hand feel. Conversely, coarser fibers create a more open structure, enhancing permeability and drainage.
- Density: The density directly correlates with the felt’s strength, thickness, and weight. Higher density felts offer better stability and durability but may have reduced permeability. Lower density felts are lighter and more permeable, ideal for applications requiring fluid flow.
- Thickness: Thickness is adjustable based on the application. Thicker felts provide better insulation and cushioning, while thinner felts are suitable for applications requiring flexibility and conformability.
- Porosity and Permeability: These properties determine the felt’s ability to allow fluids or gases to pass through. The porosity is controlled by fiber arrangement and density, impacting applications like filtration and ventilation.
- Tensile Strength: This property measures the felt’s resistance to tearing and stretching. High tensile strength is crucial for applications involving stress and strain.
- Thermal Stability: Depending on the fiber type, chemical fiber mesh felt can exhibit varying degrees of heat resistance. Some types can withstand high temperatures, while others are more susceptible to thermal degradation.
- Chemical Resistance: The resistance to chemicals varies depending on the fiber type. Some felts are resistant to acids, alkalis, and solvents, making them suitable for specific industrial processes.
Applications:
The diverse properties of chemical fiber mesh felt allow its use in a wide range of industries and applications:
- Filtration: Its porous structure makes it ideal for filtering liquids and gases in various applications, including water treatment, air filtration, and industrial processes.
- Thermal Insulation: Its ability to trap air makes it an effective thermal insulator in applications such as building insulation, automotive components, and industrial equipment.
- Acoustic Insulation: The felt’s porous structure can absorb sound waves, providing acoustic insulation in buildings, vehicles, and machinery.
- Cushioning and Padding: Its flexibility and softness make it suitable for cushioning and padding in various products, including furniture, packaging, and protective gear.
- Reinforcement: Its strength and flexibility allow it to be used as a reinforcement material in composite structures and other applications requiring structural support.
- Geotextiles: Chemical fiber mesh felt finds applications in geotechnical engineering as a separation, filtration, or drainage layer in construction projects.
- Wicking and Absorption: Certain types of chemical fiber mesh felt exhibit good wicking and absorption capabilities, making them suitable for applications like cleaning and absorbent materials.
Conclusion:
Chemical fiber mesh felt is a versatile material with a broad range of applications. By carefully selecting the fiber type, density, and thickness, manufacturers can tailor the felt’s properties to meet the specific requirements of diverse industries. Its cost-effectiveness, ease of processing, and excellent performance characteristics ensure its continued importance in various applications.