Automobiles utilize a wide variety of non – metallic materials, covering plastics, rubbers, adhesive sealants, friction materials, fabrics, and glass. The application of these materials involves multiple industrial sectors such as petrochemical, light industry, textile, and building materials. Therefore, the application level of non – metallic materials in the automotive field not only reflects a country’s comprehensive economic and technological strength but also embodies the technological development and application capabilities of numerous related industries.
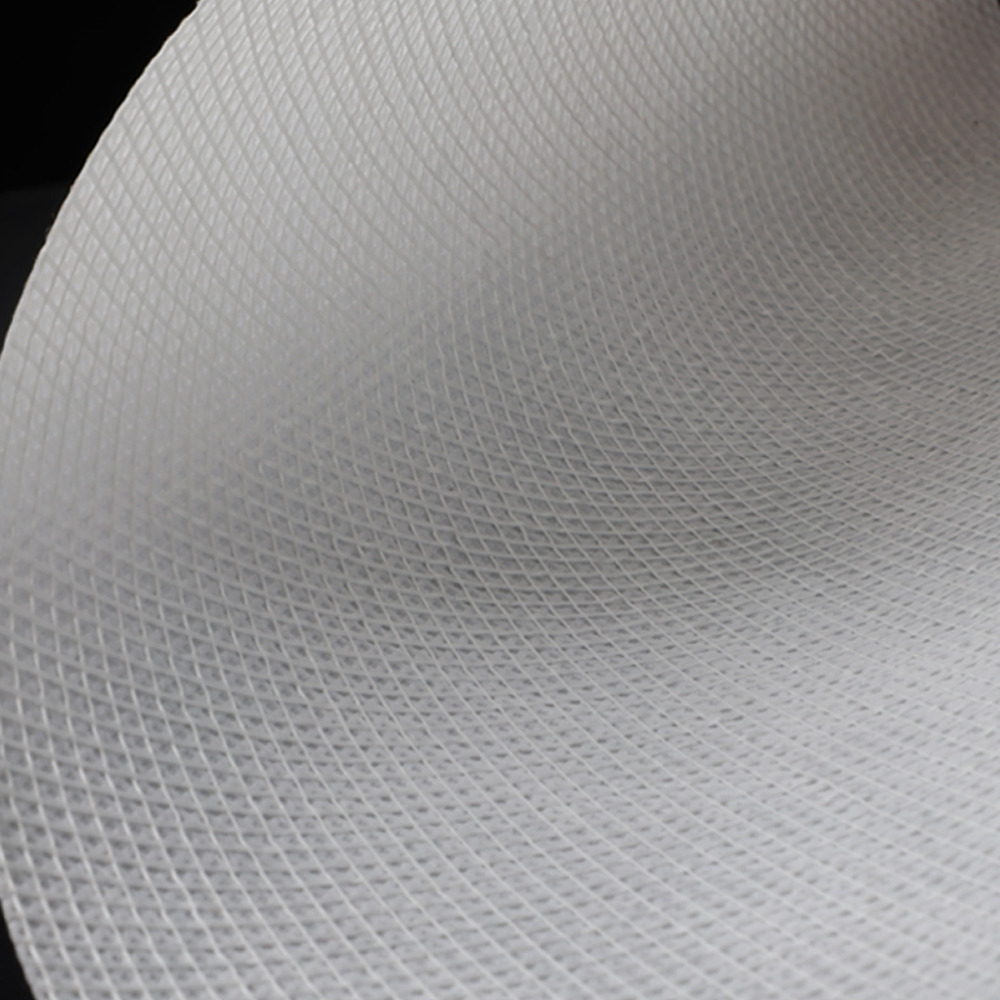
Currently, the glass fiber – reinforced composites applied in automobiles include glass fiber – reinforced thermoplastics (QFRTP), glass fiber mat – reinforced thermoplastics (GMT), sheet molding compound (SMC), resin transfer molding materials (RTM), and hand – lay – up FRP products. The commonly used glass fiber – reinforced plastics in automobiles mainly include glass fiber – reinforced PP, glass fiber – reinforced PA66 or PA6, as well as a small amount of PBT and PPO materials.
Reinforced PP is mainly used to manufacture products such as engine cooling fan blades and timing belt upper and lower covers. However, some products have problems such as poor appearance quality and warping. Therefore, non – functional parts are gradually being replaced by PP filled with inorganic fillers such as talcum powder.
Reinforced PA materials have been widely applied in both passenger cars and commercial vehicles. Generally, they are used to manufacture some small functional components, such as lock body protective covers, safety wedge blocks, embedded nuts, accelerator pedals, shift upper and lower bracket – protective covers, and opening handles. If the material quality selected by the parts manufacturer is unstable, the production process is inappropriate, or the material is not dried sufficiently, fractures are likely to occur in the weak parts of the products.
Plastic intake manifolds are a new technology developed in recent years. Compared with aluminum – alloy – cast intake manifolds, they have advantages such as light weight, smooth inner surface, shock absorption, and heat insulation. Therefore, they have been widely used in foreign automobiles. The materials used are all glass fiber – reinforced PA66 or PA6, mainly using the lost – core method or vibration friction welding method. Currently, relevant domestic units have carried out research in this area and achieved phased results.
With the increasing requirements for lightweighting and environmental protection in the automotive industry, the foreign automotive industry is increasingly inclined to use GMT materials to meet the needs of structural components. This is mainly because GMT materials have a series of advantages such as good toughness, short molding cycle, high production efficiency, low processing cost, and no environmental pollution, and are regarded as one of the important materials in the 21st century. It is mainly used to produce passenger car multi – functional brackets, instrument panel brackets, seat skeletons, engine shields, battery brackets, etc. The Audi A6 and A4 models currently produced by FAW – Volkswagen have adopted GMT materials, but local production has not been achieved yet.
In order to improve the overall quality of automobiles, catch up with international advanced levels, and achieve the goals of weight reduction, shock absorption, and noise reduction, relevant domestic units carried out research on GMT material production and product molding processes during the Eighth and Ninth Five – Year Plans and have the ability to mass – produce GMT materials. A production line with an annual output of 3000 tons of GMT materials has been built in Jiangyin, Jiangsu. Domestic automobile manufacturers have also adopted GMT materials in the design of some models and started mass – trial production.
Sheet molding compound (SMC) is an important glass fiber – reinforced thermosetting plastic. Due to its excellent performance, large – scale production capacity, and ability to achieve Class – A surfaces, it has been widely applied in automobiles. Currently, there have been new progress in the application varieties of SMC materials in automobiles abroad. Now, the largest amount of SMC used in automobiles is for body panels, accounting for 70% of SMC usage. The fastest – growing applications are in structural parts and transmission parts. It is expected that in the next five years, the usage of SMC in automobiles will continue to increase by 22% – 71%, while the growth rate in other industries will be 13% – 35%.
Foreign Application Status and Development Trends
Application of High – content Glass Fiber – reinforced Sheet Molding Compound
High – content glass fiber – reinforced sheet molding compound is increasingly being applied to automotive structural components. In 1995, Ford first demonstrated its application in structural components on the Explorer and Ranger models. Due to its multiple functions and significant advantages in structural design, it has been widely promoted and applied in automotive instrument panels, steering gears, radiator systems, and electronic device systems.
The upper and lower brackets molded by the American Budd Company use unsaturated polyester composites containing 40% glass fiber. The two – piece front – end structural design of the vehicle meets user needs. The upper bracket is fixed to the front – end roof and front – end body structure, while the lower bracket cooperates with the cooling system. These two brackets are connected to each other and, together with the roof and body structure, ensure the stability of the front – end.
Application of Low – density SMC Materials
The specific gravity of low – density SMC is 1.3. In practical applications and tests, it has been shown that it is 30% lighter than standard SMC (with a specific gravity of 1.9). Compared with similar components made of steel, using this low – density SMC can reduce the weight by about 45%.
All 1999 Corvette models of General Motors in the United States use low – density SMC for inner panels and new roof interiors. In addition, it is also used in components such as doors, engine hoods, and trunk lids. The engine hood of the American Dodge Vipex vehicle also uses this low – density SMC. Half of the 1999 models use this material to make the engine hood, and the low – density SMC engine hood is 35% lighter than steel parts.
Other Applications
In addition to the above – mentioned new applications, SMC is also used to produce some other automotive parts, such as cab doors, inflatable roofs, bumper skeletons, cargo doors, sun visors, A and D pillars, body panels, roof drain pipes, roof side rails, and truck cargo boxes. Among them, the largest amount is used for body outer panels.
Domestic Application Overview
With the introduction of domestic passenger car production technologies, SMC was first applied in passenger cars, mainly used in parts such as spare – tire compartments and bumper skeletons. Currently, it is also applied in commercial vehicles, such as tappet chamber covers, expansion tanks, wire harness clips, large/small partitions, and intake manifold assemblies.
Requirements for the Domestic SMC Material Industry
Research on Low – density SMC Materials
To better achieve the goal of automotive weight reduction, foreign countries have already started using low – density SMC to make automotive parts. According to foreign data, when comparing ordinary SMC with low – density SMC, when the density decreases from 1.9 to 1.31, the tensile strength increases from 56MPa to 80MPa, the flexural strength increases from 151MPa to 186MPa, the flexural modulus increases from 8.8GPa to 10.1GPa, and the non – notched impact increases from 925J/m to 940J/m. From these data, it can be seen that the mechanical properties of low – density SMC are generally improved. Foreign countries have actually used it to produce products such as door frames, rear – roof decorations, and engine hoods.
Recycling of SMC
Traditionally, it was believed that thermosetting composites could not be recycled. However, with the increasing importance of environmental protection, the recyclability of SMC must be considered. Data shows that both painted and bonded SMC can be recycled, and the performance of parts made from recycled SMC is not affected. Some automobile manufacturers use recycled SMC to make various components, reducing the weight of each part by 10%. For example, an engine hood made of entirely new SMC material weighs 9kg, while an engine hood made with 25% recycled material added weighs 8kg. In the near future, bumpers made from recycled SMC will be applied to heavy – duty commercial vehicles. At the same time, engine hoods, movable roof linings, side panels, grille panels, and body outer panels can also be made using recycled SMC. The recycling of SMC is a relatively new task for the domestic materials industry but is of great significance.
Other Requirements
- Promotion and Application of SMC Color Parts: This can eliminate the spraying process (including pre – and post – treatment processes) for SMC parts.
- Achievement of Class – A Surface for SMC Parts: Improve the surface quality of parts.
- Research on Low – pressure Molding Technology for SMC Parts: Explore more efficient molding processes.
The RTM method is to press resin into a closed mold with glass fibers placed inside and cure it at room temperature or by heating. Compared with the SMC method, the RTM method has simple production equipment, low mold costs, and excellent product physical properties, but it is only suitable for small – to medium – batch production. It is reported that currently, automotive parts produced by the RTM molding method abroad have been extended to full – body coverings. In China, the application of RTM molding technology in manufacturing automotive parts is still in the development and research stage, aiming to make the mechanical properties of raw materials, curing time, finished products, and other indicators reach the production levels of similar foreign products. Currently, automotive parts developed and researched by the domestic RTM molding method include air – deflector covers, rear tailgates, fairings, roofs, bumpers, and the rear lift – gates of Fukang cars.
However, in order to make the RTM process be applied to the automotive field faster and better, issues such as the requirements of materials for product structures, the level of material properties to be achieved, evaluation criteria, and the achievement of Class – A surfaces are the focuses of the automotive industry and are also the prerequisite conditions for the real promotion of RTM in automotive parts manufacturing.
Why Use Fiberglass Reinforced Plastics (FRP)
From the perspective of automobile manufacturers, compared with other materials, FRP is an extremely attractive alternative material. Taking SMC/BMC as an example, it has the following advantages:
- Weight Savings: Contributes to automotive lightweighting.
- Component Integration: Reduces the number of parts and improves overall performance.
- Design Freedom: Enables more complex designs.
- Much Less Investment: Lowers production costs.
- Making Integrated Antenna Systems a Reality: Enhances the performance of automotive electronic devices.
- Compatible with E – coat (Online Color Customization): Provides more appearance options.
- Dimensionally Stable (Low Linear Thermal Expansion Coefficient, Comparable to Steel): Ensures part accuracy.
- Maintaining High Mechanical Properties under High – temperature Conditions: Adapts to complex working environments.