In corrosive environments such as chemical plants, marine settings, and oil facilities, woven fiberglass mesh is commonly used for anti-corrosion wrapping of pipelines, storage tanks, and steel structures, replacing traditional metal mesh or simple coatings to provide long-lasting protection. Below are detailed application methods and key considerations.
1. Advantages of Fiberglass Mesh for Anti-Corrosion Wrapping
Feature | Compared to Traditional Metal Mesh/Coatings |
---|---|
Corrosion Resistance | Resists acids, alkalis, salt spray, and chemicals; does not rust (unlike metal mesh). |
Lightweight | Weighs only 1/4 of metal mesh, reducing structural load. |
Easy Installation | Flexible, conforms to complex surfaces, no welding required. |
Electrical Insulation | Non-conductive, suitable for electrical equipment protection. |
High-Temperature Resistance | Withstands -60°C to 550°C long-term, up to 1000°C short-term (e.g., high-temperature pipelines). |
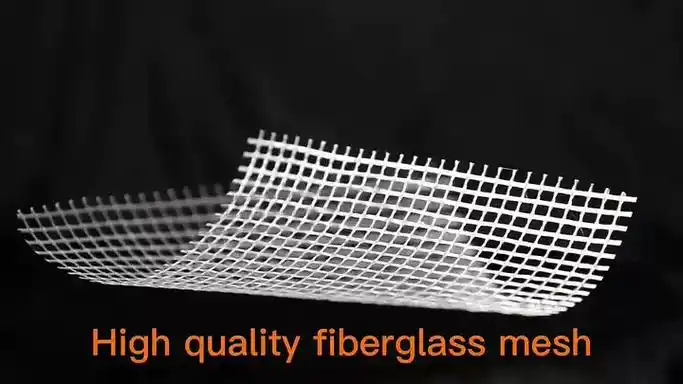
2. Common Applications
- Chemical Pipelines/Tanks: Protects against acids, alkalis, and organic solvents.
- Marine Structures: Prevents seawater corrosion on dock pilings and ship hulls.
- Oil Rigs: Wrapping for oil/gas pipelines resistant to hydrogen sulfide (H₂S).
- Wastewater Treatment: Protects steel structures in aeration tanks and sedimentation basins.
3. FAQs & Troubleshooting
Q1: Can fiberglass mesh be applied on damp surfaces?
- Substrate must be dry (≤8% moisture). For emergencies, use moisture-cure epoxy.
Q2: How to test wrapping quality?
- Spark Test: Detects pinholes (adjust voltage per thickness).
- Adhesion Test: Cross-cut (ASTM D3359) or pull-off testing.
Q3: Expected service life?
- Mild environments (indoor pipes): 10–15 years.
- Harsh conditions (chemical/marine): 5–8 years (regular inspections needed).
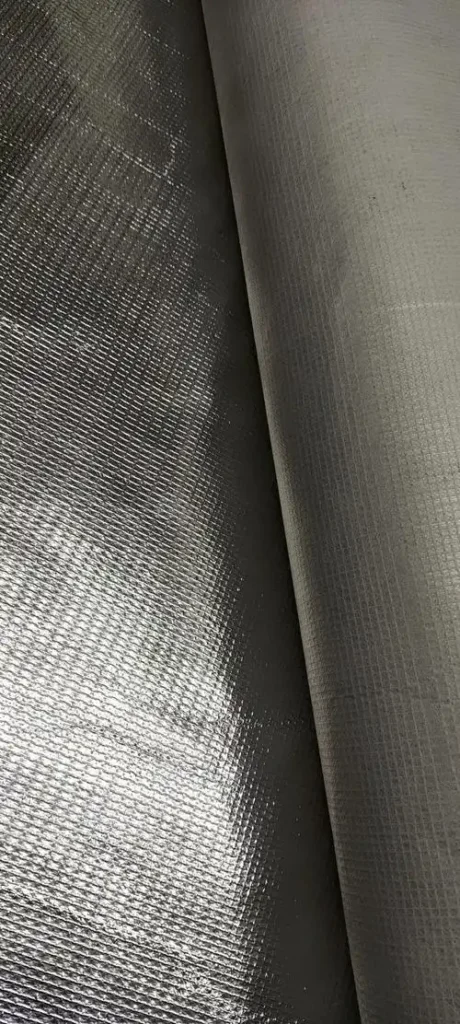