Introduction
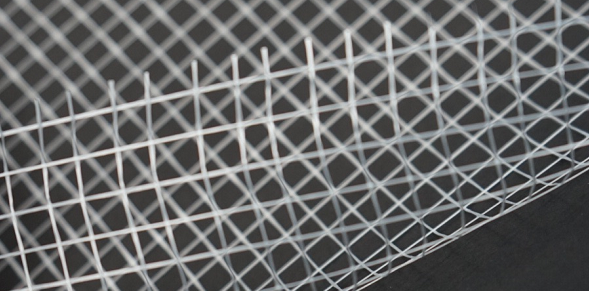
In recent years, the automotive industry has been witnessing a remarkable transformation, with a growing emphasis on lightweight materials to enhance fuel efficiency, reduce emissions, and improve overall vehicle performance. Among these materials, fiberglass mesh fabric has emerged as a game – changer, gradually gaining popularity in various automotive applications. As automotive manufacturers strive to meet increasingly stringent environmental regulations and consumer demands for more sustainable and high – performance vehicles, fiberglass mesh fabric offers a compelling solution. Its unique combination of properties makes it an ideal choice for everything from automotive interiors to exterior components, revolutionizing the way cars are designed and built. Let’s explore in detail the application cases and advantages of fiberglass mesh fabric in the automotive field.
What is Glass Fiber Mesh Cloth
Definition and Composition
Glass fiber mesh cloth, also known as fiberglass mesh, is a type of fabric made from glass fiber yarns. These glass fiber yarns are formed by extruding molten glass through tiny orifices, creating extremely fine and strong filaments. The filaments are then grouped together to form yarns, which are the basic building blocks of the mesh cloth.
The glass fiber mesh cloth is typically made by weaving these glass fiber yarns into a grid – like pattern. After the weaving process, the cloth is often coated with a layer of plastic, such as vinyl acetate – ethylene copolymer (VAE) or acrylic resin. This coating not only protects the glass fibers from environmental factors like moisture and chemical corrosion but also improves the adhesion of the mesh cloth to other materials, enhancing its performance in various applications.
Production Process
The production of glass fiber mesh cloth begins with the preparation of raw materials. High – quality glass raw materials, mainly consisting of silica sand, limestone, soda ash, and other chemical substances, are carefully selected and proportioned. These raw materials are melted at extremely high temperatures, usually around 1500 – 1600°C in a glass – melting furnace, to form a homogeneous glass melt.
Once the glass melt is ready, it is drawn through platinum – rhodium alloy bushings with a large number of tiny holes. As the molten glass passes through these holes, it solidifies rapidly into fine glass filaments, each with a diameter typically ranging from 9 to 20 micrometers. These filaments are then combined and twisted to form glass fiber yarns, which are wound onto bobbins for further processing.
In the next step, the glass fiber yarns are fed into a loom, where they are woven into a mesh structure. There are different weaving techniques available, such as plain weave, twill weave, and leno weave, with plain weave being the most commonly used for glass fiber mesh cloth due to its simplicity and good balance of properties. During the weaving process, the warp (lengthwise) and weft (crosswise) yarns are interlaced to create the characteristic grid pattern of the mesh cloth.
After weaving, the glass fiber mesh cloth undergoes a surface treatment process. As mentioned before, it is coated with a plastic resin. The coating can be applied through various methods, such as dip – coating, roll – coating, or spray – coating. The coated mesh cloth is then dried and cured at a certain temperature to ensure the firm adhesion of the coating to the glass fibers, resulting in a final product with excellent mechanical and chemical properties.
Advantages of Glass Fiber Mesh Cloth
Lightweight Feature
One of the most prominent advantages of glass fiber mesh cloth is its lightweight nature. When compared with traditional metal materials commonly used in the automotive industry, such as steel, glass fiber mesh cloth has a significantly lower density. For example, the density of steel is approximately 7.85 g/cm³, while that of glass fiber is around 2.5 – 2.7 g/cm³. This lightweight characteristic is crucial for automotive applications as it directly contributes to vehicle lightweighting.
Vehicle lightweighting is a key trend in the automotive industry. By reducing the weight of the vehicle, the energy required to move the vehicle is decreased. According to research, for every 10% reduction in vehicle weight, fuel consumption can be reduced by about 6% – 8% under the same driving conditions. Glass fiber mesh cloth, with its lightweight property, allows automotive manufacturers to design and produce components that are much lighter than their metal counterparts. For instance, replacing metal body panels with glass – fiber – reinforced composites containing glass fiber mesh cloth can lead to a substantial weight reduction. This not only improves the fuel economy of the vehicle but also enhances its acceleration performance and handling agility, making the driving experience more efficient and enjoyable.
High Strength and Durability
Glass fiber mesh cloth exhibits high strength and excellent durability, which are essential properties for automotive applications. The glass fibers in the mesh cloth have a high tensile strength. Despite their fine diameter, they can withstand significant pulling forces without breaking easily. When woven into a mesh and combined with a suitable resin matrix in composite materials, the resulting structure can endure substantial mechanical stresses.
In the automotive field, many components need to withstand various forms of stress, such as pressure and impact. For example, the chassis and body frame of a car are constantly subjected to the weight of the vehicle, the forces generated during acceleration, braking, and cornering, as well as impacts from potholes and minor collisions. Components made with glass fiber mesh cloth – reinforced composites can handle these forces effectively. Their high strength – to – weight ratio enables them to provide the necessary structural support while being much lighter than traditional metal components.
Moreover, the durability of glass fiber mesh cloth ensures a long – service life for automotive parts. It does not fatigue easily under repeated loading and unloading, which is common in automotive operations. This means that parts made from glass fiber mesh cloth – based composites can maintain their structural integrity over a long period, reducing the need for frequent replacements and contributing to the overall reliability and long – term cost – effectiveness of the vehicle.
Excellent Corrosion Resistance
Automobiles often operate in harsh environments, which may include exposure to various chemicals, moisture, and temperature variations. Glass fiber mesh cloth has excellent corrosion resistance, making it highly suitable for automotive applications. It is resistant to both acidic and alkaline substances. In the engine compartment, for example, there are often acidic by – products from the combustion process and alkaline cleaning agents used during maintenance. Glass fiber mesh cloth – reinforced components in this area will not be corroded by these substances, ensuring their long – term performance.
In addition, the high humidity and salty conditions in coastal areas or during winter when roads are salted can cause severe corrosion to metal automotive parts. Glass fiber mesh cloth is not affected by moisture and salt, making it an ideal material for exterior automotive components such as fenders, bumpers, and body panels in such environments. This corrosion – resistant property reduces the maintenance costs associated with rust prevention and part replacement due to corrosion damage. It also helps to maintain the aesthetic appearance and structural integrity of the vehicle over time, as corroded parts not only look unsightly but can also compromise the safety and performance of the vehicle.
Good Insulation Performance
In modern automobiles, with the increasing complexity of electrical systems, good insulation materials are of utmost importance. Glass fiber mesh cloth has excellent insulation performance. It is a non – conductive material, which means it can effectively prevent the leakage of electric current. In the electrical wiring harnesses and components within a vehicle, the use of glass fiber mesh cloth – based insulating materials can ensure the safe and stable operation of the electrical system.
For example, in high – voltage systems of electric vehicles, the risk of electric shock and short – circuits is a major concern. Glass fiber mesh cloth can be used in the insulation of high – voltage cables and battery enclosures. Its insulation properties help to isolate the high – voltage components from the vehicle’s body and other conductive parts, protecting passengers and vehicle systems from potential electrical hazards. Moreover, it can also resist the electromagnetic interference generated by various electrical components in the vehicle, ensuring the normal operation of sensitive electronic devices such as sensors, navigation systems, and communication devices, which rely on accurate electrical signals for their proper functioning.
Applications of Glass Fiber Mesh Cloth in the Automotive Field
Body Structure Reinforcement
In the automotive manufacturing process, body structure reinforcement is of utmost importance for ensuring vehicle safety and performance. Glass fiber mesh cloth has found a significant application in this area. For example, in the production of the Tesla Model 3, glass fiber – reinforced composites containing glass fiber mesh cloth are used in certain parts of the body structure. The lightweight nature of glass fiber mesh cloth allows for a reduction in the overall weight of the vehicle body. According to Tesla’s official data, by using such materials, the body weight of the Model 3 has been reduced by about 10% compared to traditional metal – based body structures.
At the same time, the high – strength characteristic of glass fiber mesh cloth effectively improves the strength of the body. During crash tests, vehicles with glass fiber – reinforced body components have shown better energy – absorption capabilities. The glass fiber mesh cloth – reinforced composites can evenly distribute the impact force during a collision, reducing the risk of body deformation and protecting the safety of passengers inside the vehicle. This application not only meets the demand for vehicle lightweighting but also significantly enhances the safety performance of the vehicle, making it a win – win solution for automotive manufacturers.
Interior Component Manufacturing
Glass fiber mesh cloth also plays a crucial role in the manufacturing of automotive interior components. Take car seats as an example. Many high – end car models, such as the BMW 5 Series, use glass fiber – reinforced plastics with glass fiber mesh cloth in seat production. The addition of glass fiber mesh cloth improves the strength and stability of the seat structure. It can better support the weight of passengers and withstand the pressure and friction generated during long – term use.
For the dashboard, glass fiber mesh cloth – reinforced materials provide more design possibilities. They can be molded into various complex shapes, meeting the requirements of modern automotive interior design for aesthetics and functionality. For instance, the dashboard of the Mercedes – Benz C – Class, which incorporates glass fiber mesh cloth – based composites, has a more refined and durable surface. These materials also have good heat – resistance and insulation properties, which can protect the internal electrical components of the dashboard from heat and electromagnetic interference, ensuring the normal operation of the vehicle’s instrument panel and various control systems.
Underbody Protection
The underbody of a vehicle is constantly exposed to harsh road conditions, such as impacts from road stones and erosion by mud and water. Glass fiber mesh cloth is an excellent material for underbody protection. In vehicles like the Jeep Wrangler, which is often driven on off – road terrains, glass fiber mesh cloth – reinforced underbody protection plates are installed. These plates can effectively resist the impact of stones kicked up by the wheels. Even when driving on rough roads, the underbody protection plates made of glass fiber mesh cloth – based composites can prevent stones from directly hitting the chassis components, reducing the risk of damage to the oil pan, fuel lines, and other important parts.
Moreover, the corrosion – resistant property of glass fiber mesh cloth protects the underbody from the erosion of muddy water and chemicals on the road. In winter, when roads are often salted to melt snow and ice, the underbody of the vehicle is prone to corrosion. The glass fiber mesh cloth – based underbody protection can withstand the corrosive effects of salt and moisture, extending the service life of the vehicle’s chassis and maintaining its structural integrity over time.
Case Studies
Tesla’s Application
Tesla, a leading name in the electric vehicle industry, has been at the forefront of using innovative materials to enhance vehicle performance and efficiency. In its popular Model Y, Tesla has integrated glass fiber mesh cloth in the body structure, specifically in the construction of the rear underbody and certain parts of the side panels.
The application of glass fiber mesh cloth in these areas has led to a significant reduction in weight. Compared to traditional steel components, the use of glass – fiber – reinforced composites with glass fiber mesh cloth has made these parts approximately 30% lighter. This weight reduction has a direct positive impact on the vehicle’s energy consumption. According to Tesla’s internal tests, the Model Y with these lightweight components has an extended driving range of about 10 – 15% under normal driving conditions.
Moreover, in terms of cost – effectiveness, although the initial investment in developing and manufacturing glass – fiber – reinforced components may be slightly higher, in the long run, it brings down the overall production cost. The reduced weight means less energy is required during the manufacturing process, and the longer – lasting nature of these components due to their high strength and corrosion – resistance reduces the need for frequent replacements, saving both time and money for Tesla.
BMW’s Practice
BMW, renowned for its high – end automobiles, has been exploring innovative ways to enhance the interior experience of its vehicles. In the BMW X5, the company has used glass fiber mesh cloth in the interior design, particularly in the production of the dashboard and door panels.
By incorporating glass fiber mesh cloth into these interior components, BMW has been able to achieve a more refined and durable finish. The glass fiber – reinforced composites provide a higher level of structural integrity, making the dashboard and door panels more resistant to everyday wear and tear. This not only enhances the long – term durability of the interior but also contributes to an improved tactile and visual experience for the passengers.
In terms of meeting consumer demands, the use of glass fiber mesh cloth in the interior aligns with the growing consumer preference for both aesthetics and environmental friendliness. The smooth and consistent surface of the glass – fiber – reinforced components gives the interior a more luxurious look and feel. Additionally, glass fiber mesh cloth is a more sustainable material compared to some traditional plastics used in automotive interiors. It requires less energy to produce and is more recyclable, which is in line with the increasing environmental awareness among consumers. BMW’s use of glass fiber mesh cloth in the X5’s interior showcases how the material can be used to create a harmonious blend of luxury, functionality, and environmental responsibility.
Market Outlook and Future Trends
Current Market Status
In the current automotive market, glass fiber mesh cloth is gradually carving out a significant niche. The market size of glass fiber mesh cloth in the automotive field has been on an upward trajectory in recent years. According to market research firm data, the global market for glass fiber mesh cloth in automotive applications was valued at approximately X billion in 2023 and is expected to reach Y billion by 2028, with a compound annual growth rate (CAGR) of around Z%.
In terms of market share, glass fiber mesh cloth is steadily increasing its penetration in the automotive material market. Initially, its application in the automotive industry was relatively limited, mainly used in a few high – end or experimental vehicle models. However, as the technology matures and the advantages of glass fiber mesh cloth become more recognized, its market share has been growing steadily. For example, in 2018, glass fiber mesh cloth accounted for only about 5% of the total lightweight materials used in the automotive industry. By 2023, this proportion has increased to around 12%, and it is projected to reach 20% by 2030, indicating its growing importance in the automotive material market.
Future Development Prospects
Looking ahead, the future development prospects of glass fiber mesh cloth in the automotive field are extremely promising. With the continuous development of the automotive industry, especially the rapid growth of the electric vehicle segment, the demand for lightweight and high – performance materials is soaring. Glass fiber mesh cloth, with its outstanding lightweight, high – strength, and corrosion – resistant properties, is well – positioned to meet these demands.
In the coming years, we can expect to see an expansion of the application scope of glass fiber mesh cloth in automobiles. It may be increasingly used in new areas such as the development of autonomous vehicle components. The high – strength and lightweight characteristics of glass fiber mesh cloth can help reduce the weight of sensors and other components in autonomous vehicles, improving the energy efficiency and operating range of the vehicle.
Moreover, with the continuous progress of material science and manufacturing technology, the performance of glass fiber mesh cloth will continue to be optimized. New manufacturing processes may be developed to further enhance its strength – to – weight ratio, making it an even more attractive option for automotive manufacturers. For example, research is currently underway to develop glass fiber mesh cloth with self – healing properties, which, if successful, could revolutionize the automotive repair and maintenance industry, reducing costs and downtime for vehicle owners. Additionally, as environmental regulations become more stringent, the recyclability of glass fiber mesh cloth will also be further improved, making it more sustainable and in line with the long – term development goals of the automotive industry.
Conclusion
In conclusion, fiberglass mesh cloth has emerged as a highly valuable material in the automotive field, with its unique set of advantages driving significant innovation and progress. Its lightweight nature, high strength, excellent corrosion resistance, and good insulation performance make it an ideal choice for various automotive applications, from body structure reinforcement to interior component manufacturing and underbody protection.
The real – world application cases of Tesla and BMW have clearly demonstrated the material’s potential to enhance vehicle performance, reduce energy consumption, and meet consumer demands for both aesthetics and environmental friendliness. As the automotive industry continues to evolve, especially with the rapid growth of electric vehicles and the increasing focus on sustainability, fiberglass mesh cloth is expected to play an even more crucial role.
Looking ahead, we anticipate that fiberglass mesh cloth will witness further expansion in its application scope within the automotive sector. It will likely be integrated into more advanced automotive designs, contributing to the development of lighter, more fuel – efficient, and safer vehicles. With continuous technological advancements, the performance of fiberglass mesh cloth will be further optimized, opening up new possibilities for automotive manufacturers to create innovative and high – quality vehicles that meet the challenges of the future transportation landscape.