Imagine a thin sheet of aluminum foil – shiny, lightweight, but easy to tear. Now imagine a net made of very fine glass threads – strong and fireproof, but full of holes. Bond them together and you get a material far tougher and more useful than either one alone. This unlikely pairing is used in everything from building insulation to specialized packaging.
What is Glass Fiber Mesh?
Glass fiber mesh is a fabric made from extremely thin glass fibers. Fiberglass, as it’s often called, starts as molten glass that is pulled into hair-like strands and then woven into a grid-like cloth. The result looks a bit like netting or gauze, but it’s made of glass. You might have seen fiberglass mesh as the tape on drywall joints or as reinforcement in stucco walls. It’s lightweight, doesn’t stretch much, and won’t rot or burn because it’s made from inorganic glass. Even though it’s glass, it isn’t brittle – the fibers are so thin they can flex a little, giving the mesh a cloth-like toughness.
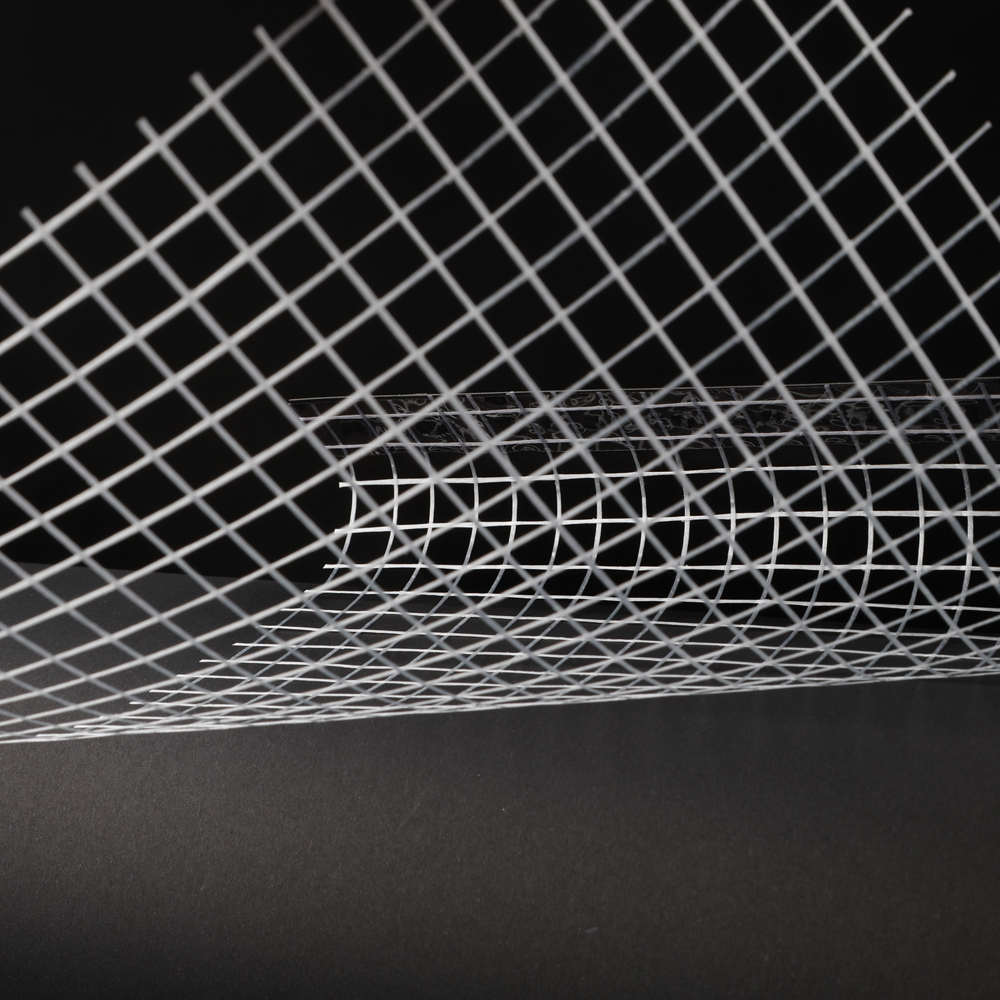
Why Combine Glass Fiber Mesh with Aluminum Foil
Pairing glass fiber mesh with aluminum foil works well because each material complements the other. The mesh gives the foil strength, and the aluminum foil provides a continuous barrier that the mesh alone lacks. Key properties of fiberglass mesh that make it an ideal foil reinforcement such as high strength and tear resistance, heat and fire resistance etc. The glass fiber mesh acts like a skeletal support for the foil. On its own, thin aluminum foil can rip easily. but the embedded glass fibers stop tears from spreading and make the laminated foil much tougher. Fiberglass also doesn’t burn, and aluminum foil won’t ignite. Together, a foil-fiberglass laminate can withstand high heat and direct flames without failing. It adds toughness, fire resistance, and stability, while the aluminum foil contributes its reflective, insulating, and sealing qualities. Using them together addresses the weaknesses each would have alone.
Benefits of the Foil and Mesh Combination
Laminating aluminum foil with fiberglass mesh yields a material that performs better than either component on its own. Aluminum foil reflects heat very effectively – it can bounce back up to 97% of radiant heat. Backing it with fiberglass creates an even better insulator. For example, a foil-fiberglass radiant barrier in an attic can reflect heat away and keep the space cooler.
Both aluminum foil and glass fiber are non-combustible, so together they form a highly fire-resistant layer. The fiberglass won’t burn, and the foil blocks direct exposure to flames, protecting whatever is behind it.
The fiberglass mesh greatly boosts the tear and puncture resistance of the foil. The laminated material can handle pulling and abrasion without ripping, unlike plain foil. This durability means it holds up well during installation and over time.
Aluminum foil is impervious to water and vapor, and the fiberglass mesh won’t deteriorate with moisture. Unlike paper-based insulation facings, it doesn’t get soggy or support mold. This laminate makes an excellent vapor barrier. It’s also chemically stable – it resists most acids, salts, and other corrosive chemicals, so it won’t degrade easily.
Also, despite its reinforcement, the foil-fiberglass material remains very lightweight. It’s easy to carry, cut, and attach with basic tools, which is convenient for builders and installers.
Common Applications
The combination of aluminum foil and fiberglass mesh is used in many applications, including building insulation, HVAC pipes, thermal packaging and fire blankets. Industrial or not, it is commonly used to enhance the end product’s durability and performance, make it able to withstand in harsh environments.
Building Insulation
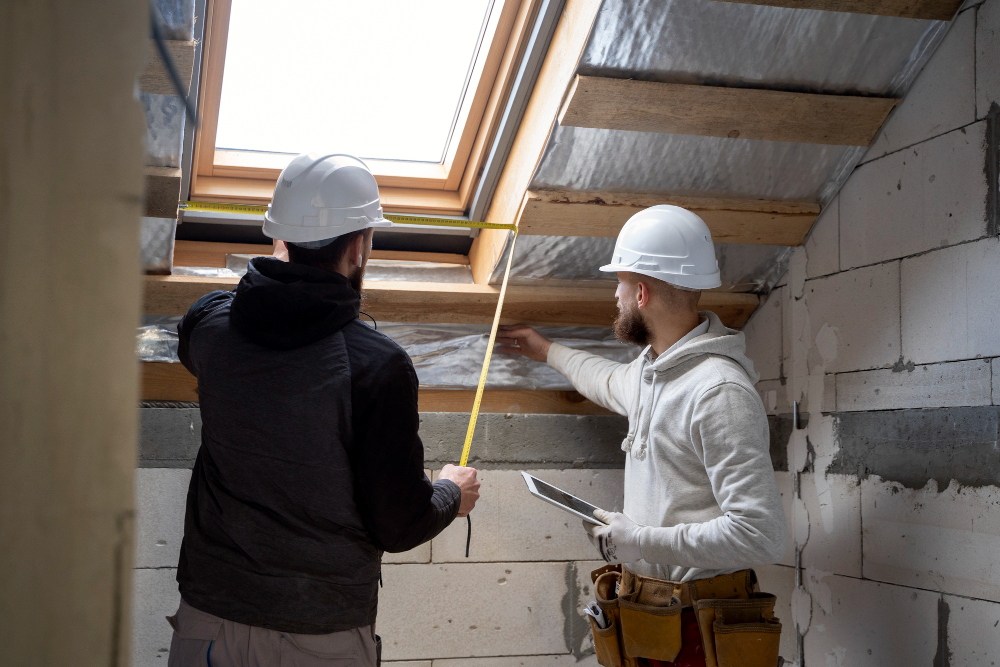
Many insulation products for homes and buildings use foil-faced fiberglass laminates. For example, fiberglass insulation batts and foam boards often have a foil-scrim facing – a shiny foil layer reinforced with fiberglass mesh – that serves as a radiant heat reflector and vapor barrier. The mesh inside the foil prevents it from ripping during installation. Attic radiant barriers are another example, where foil is bonded to mesh so it can span large areas without tearing.
HVAC Pipes
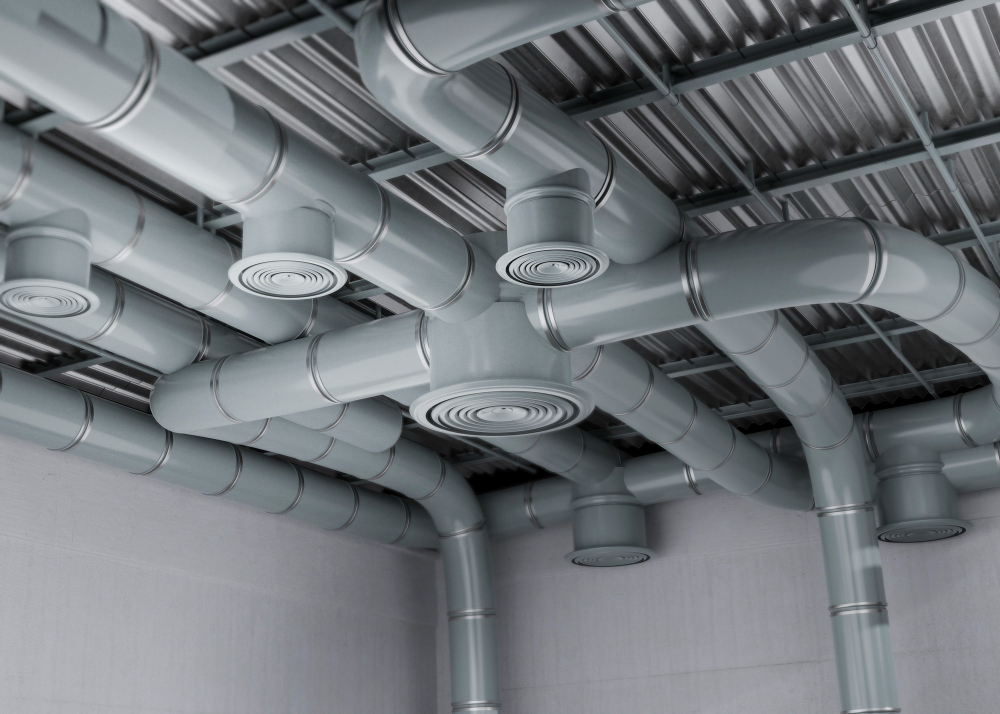
Heating and air conditioning ducts are commonly wrapped in insulation with a foil-scrim facing. The foil reflects heat and acts as a moisture seal, while the mesh adds tear resistance as the ducts vibrate or are moved. Installers also use FSK tape to seal the joints of duct insulation – the fiberglass scrim in the tape gives it strength so it won’t tear off or peel.
Fire Blankets and Curtains
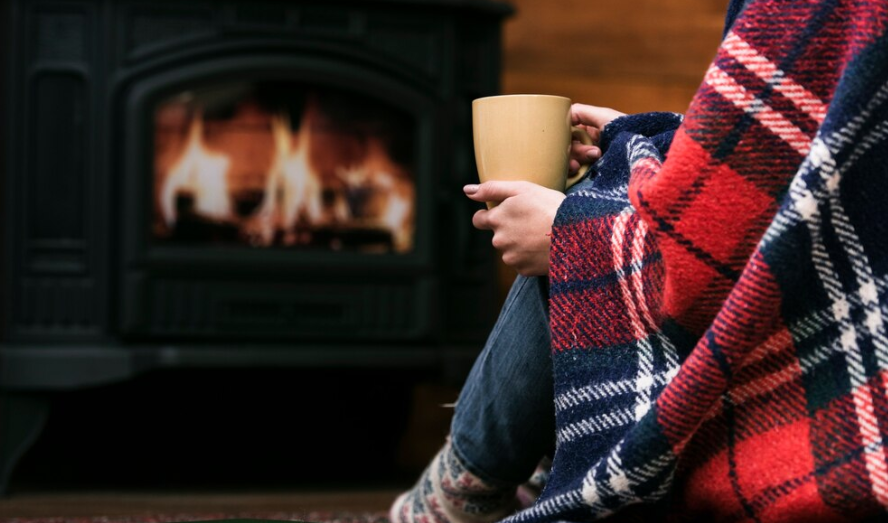
Emergency fire blankets and welding curtains often consist of foil-laminated fiberglass fabric. The foil reflects intense heat while the fiberglass cloth won’t burn, so the blanket or curtain doesn’t fail even under direct flames.
Thermal Packaging
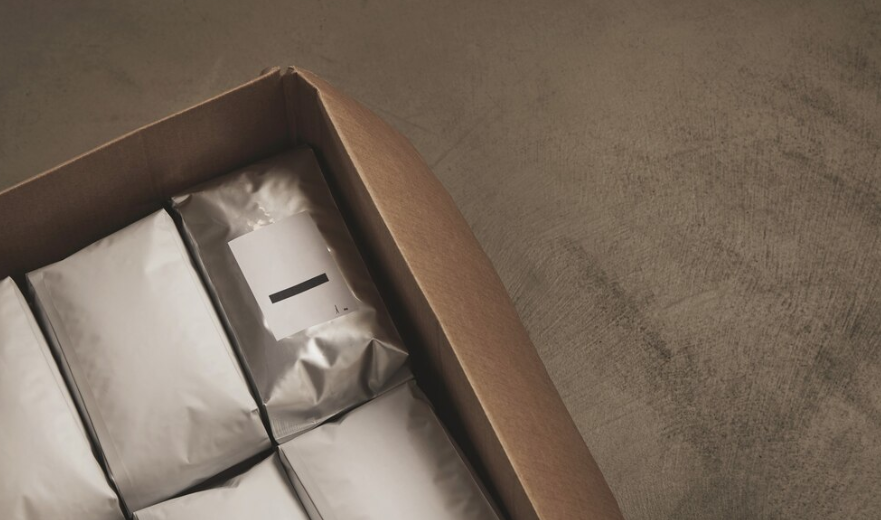
Specialized packaging materials use foil-fiberglass laminates to protect contents from heat and moisture. For instance, insulated box liners for shipping food or medicine have a reflective foil layer to fend off external heat and a fiberglass-reinforced backing for strength. Unlike plain foil that would tear, these reinforced foil wraps can withstand rough handling during transit.
Each material alone has limitations: aluminum foil is a great barrier but is fragile, while fiberglass mesh is strong but not a barrier. Laminating them together solves both issues. The foil provides a shield against heat, fire, and moisture, and the mesh makes that shield tough and tear-resistant. In essence, the foil keeps out what it needs to keep out, and the fiberglass mesh makes sure the foil stays intact. This synergy makes the combined material far more effective and durable than either material on its own.