Fiber Reinforced Plastic (FRP) pipeline systems have become a popular choice in industries such as water supply, oil & gas, and chemical processing due to their corrosion resistance and high strength-to-weight ratio. These composite pipes consist of a polymer matrix reinforced with fibrous materials like glass fiber. To further enhance the structural integrity of FRP pipelines, manufacturers often incorporate additional reinforcement layers. One such reinforcement is laid scrim, an open-mesh fabric that is embedded within the pipe wall. Laid scrim may not be as well-known as traditional fiberglass rovings’ or mats, but it plays a critical role in improving the performance and longevity of FRP pipes. We will briefly introduce you what laid scrim is and how it is used during FRP pipeline production.
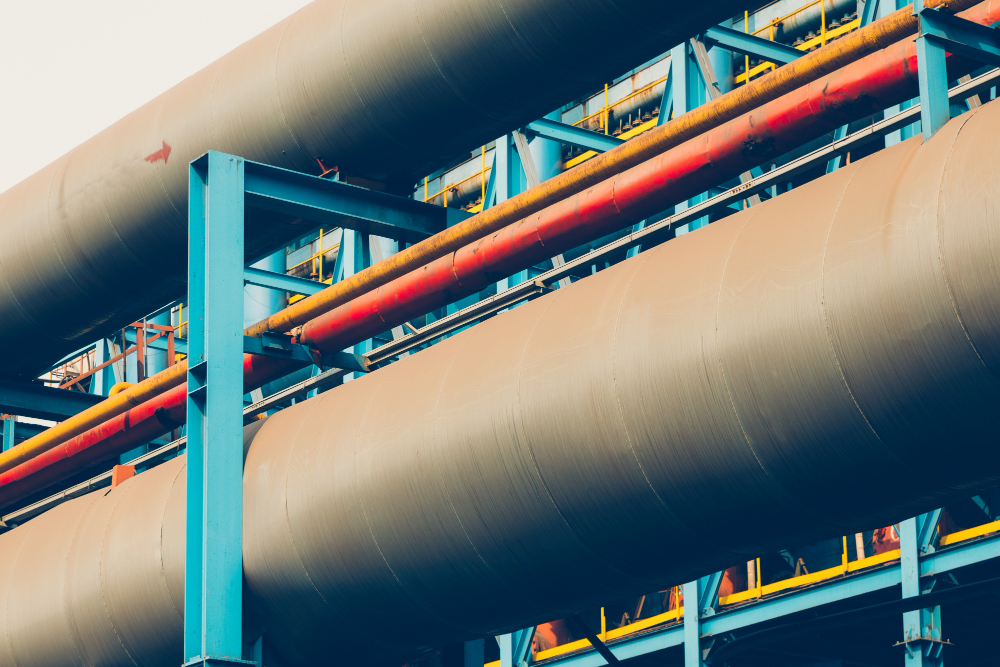
What is Laid Scrim?
First things first, laid scrim is a type of reinforcing fabric made from continuous filament yarns arranged in a grid pattern. In a laid scrim the yarns are simply laid out in different directions and bonded at their intersections. The scrim’s open structure and bonding process grants it its unique characteristics: it has high tensile strength and tear resistance while being extremely lightweight at the same time. Its unique characteristics makes it capable of withstanding harsh environments and difficult surroundings. When it comes to pipeline manufacturing, typical scrim for FRP pipelines can significantly boost the composite’s strength and dimensional stability while weight only 5-20 grams. It can bond easily with the resin, becoming fully encapsulated in the hardened plastic.
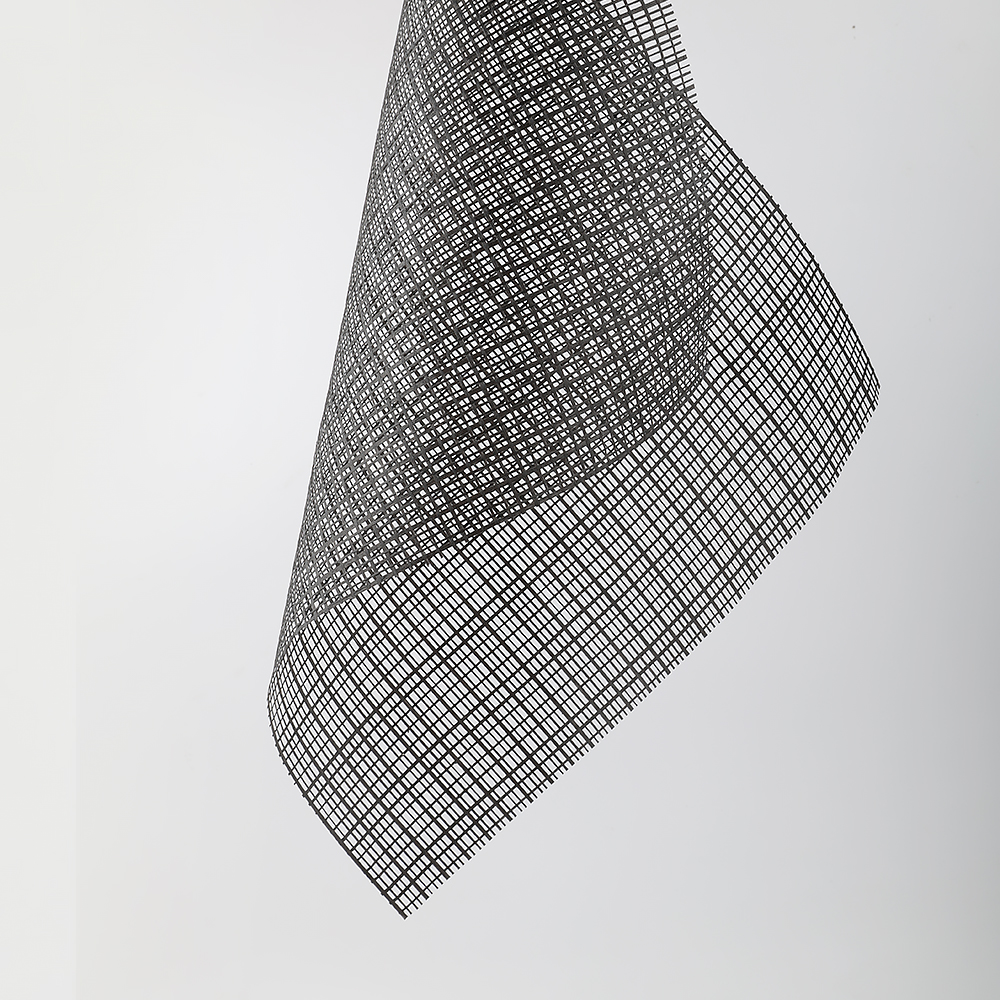
How Laid Scrim is incorporated in Pipe Manufacturing
During FRP pipe production, laid scrim is introduced as one of the reinforcement layers in the composite wall. FRP pipes are commonly manufactured by processes like filament winding or centrifugal casting. In a filament winding process, fiberglass rovings’ impregnated with resin are wound around a mandrel to build up the pipe wall. At specific stages in this winding sequence, a roll of scrim fabric is fed onto the mandrel and wrapped around the circumference of the pipe, typically on top of a wet resin layer so that the scrim gets saturated.
Once in place, additional resin and fiber layers are added on top of the scrim, and the entire assembly is cured. The scrim thus becomes embedded within the laminated wall of the pipe. Because its unique structures, the scrim will not create a impermeable barrier between laminate layers which makes resin can flow through the openings and fully encapsulate the scrim without any problems. By incorporating laid scrim into pipe manufacturing, it allows air bubbles and excess resin to pass through, helping to prevent voids. Once the pipe is cured and removed from the mandrel, the scrim is locked in place as a permanent reinforcement within the pipe wall. It becomes an integral part of the composite when fully bonded, sharing the load with fiberglass filaments and resin.
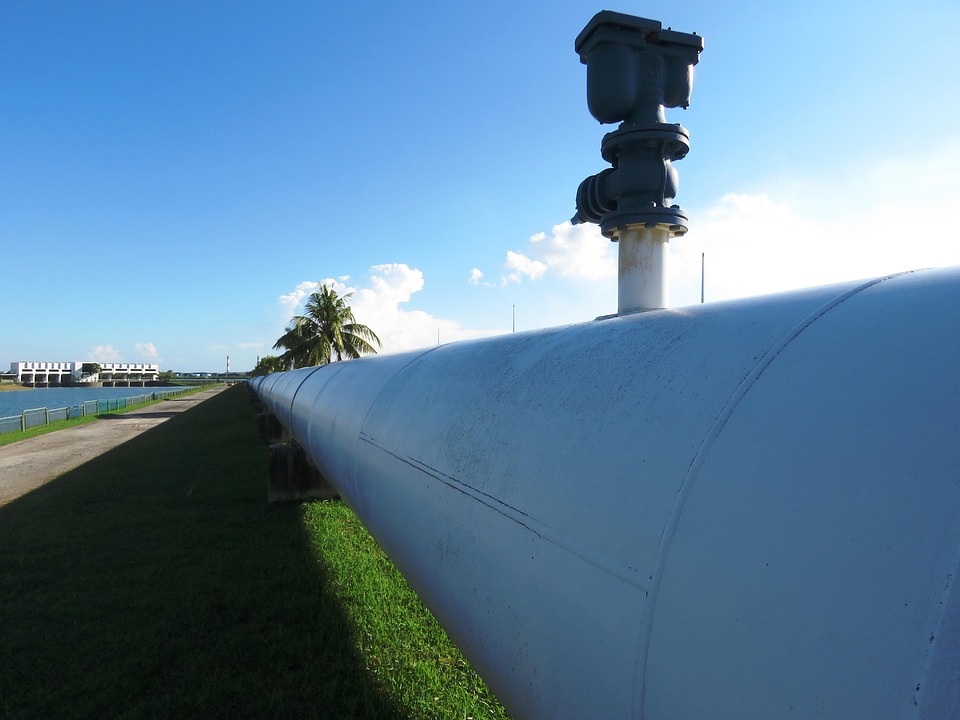
Contributions to Structural Integrity and Performance
Laid Scrim may appear as a simple mesh, but it provides multiple mechanical benefits to an pipeline. By acting as a skeletal framework within the pipe wall, scrim enhances both the strength and toughness of the composite structure. We will now demonstrate some of the key ways in which laid scrim reinforcement is contributes to the product’s structural integrity and performance.
When loads are applied to an Pipe, the presence of a scrim helps distribute these stresses more uniformly through the resin matrix. The scrim’s network of fibers takes up load and prevents stress concentrations in the resin or at fiber discontinuities.
A major benefit of scrim is its ability to arrest cracks and prevent layer separation. FRP pipes can be vulnerable to micro-cracking of the resin or delamination between fiber layers, especially under cyclic loading or impact. The open mesh essentially acts like a safety net; any cracks propagating in the resin will encounter the scrim, which blunts and halts their growth.
Laid scrim improves the dimensional stability of FRP pipes, meaning the pipe retains its shape and size more consistently under load or temperature changes. The scrim mesh acts like a skeletal framework that prevents excessive creep or deformation of the resin. Pipes reinforced with scrim have been observed to have good uniformity and expansibility – they expand or contract in a controlled, uniform manner rather than unevenly .
The open mesh of the scrim significantly raises the composite’s tear resistance. If an pipe wall incurs a small puncture or cut, a plain laminated structure might allow that damage to propagate, whereas a scrim-reinforced structure will tend to stop the tear from growing . The scrim strands physically hold the material together, requiring much more energy to rip through the mesh.
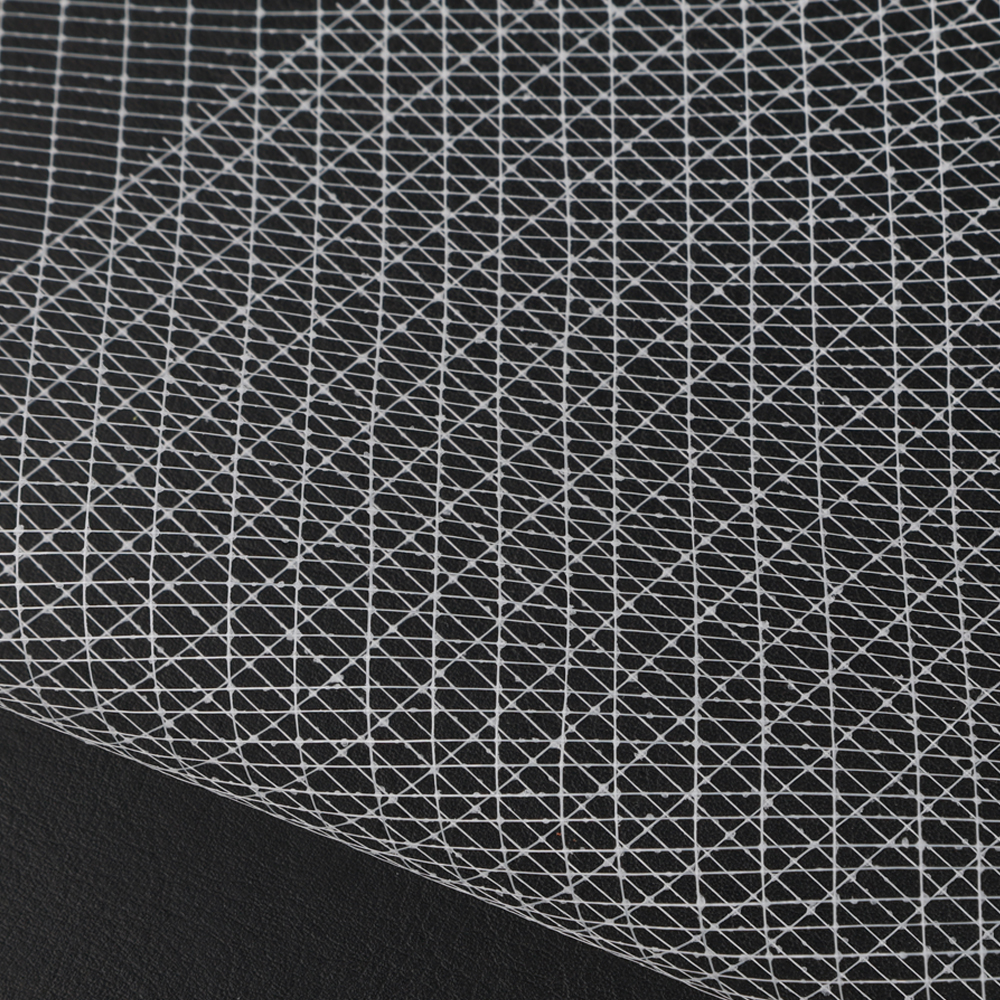
All of these effects contribute to a longer service life for the pipeline. By improving strength, distributing stress, and preventing internal damage mechanisms, scrim reinforcement helps FRP pipes stay in service longer with fewer repairs, makes an already strong composite even more robust and reliable for critical infrastructure. Laid scrim may be a hidden component within an FRP pipeline, but its impact on performance is significant.
From large infrastructure projects to no-dig pipeline repairs, laid scrim has proven to be a cost-effective solution for reinforcing plastic pipes without sacrificing weight or flexibility. As composite technology continues to advance, we can expect laid scrim and similar reinforcements to play an increasingly important role in building durable, high-performance pipeline systems for the future.