Latest News and Developments in the Fiberglass Mesh Industry
1. Introduction
Fiberglass mesh, made from fiberglass yarns woven into a grid pattern and often coated with special polymers, has emerged as a versatile and essential material across various industries. Its unique combination of high strength, excellent chemical resistance, and dimensional stability makes it a preferred choice for applications ranging from construction to aerospace. This article delves into the latest news, market trends, technological advancements, and key applications of fiberglass mesh, providing a comprehensive overview of this dynamic industry.
2. Market Trends
The global fiberglass mesh market has been on a steady growth trajectory in recent years and is expected to continue its upward trend. According to a report by [Market Research Firm Name], the market size was valued at [X] billion dollars in 2024 and is projected to reach [X] billion dollars by 2030, with a compound annual growth rate (CAGR) of [X]% during the forecast period. This growth is primarily driven by the increasing demand for high-performance building materials, the expansion of the construction industry in emerging economies, and the growing use of fiberglass mesh in industrial applications.
2.2 Regional Analysis
Regionally, Asia-Pacific dominates the fiberglass mesh market, accounting for the largest share in terms of both production and consumption. The rapid urbanization, infrastructure development, and government initiatives promoting sustainable construction in countries like China, India, and Southeast Asian nations are fueling the demand for fiberglass mesh in the region. In China alone, the construction of new residential and commercial buildings, as well as the renovation of existing structures, has led to a significant increase in the use of fiberglass mesh for applications such as wall reinforcement, waterproofing, and thermal insulation.
Europe and North America also hold significant market shares, with a focus on advanced applications in the automotive, aerospace, and renewable energy sectors. The stringent building codes and regulations in these regions, which emphasize energy efficiency and structural integrity, are driving the adoption of high-quality fiberglass mesh products.
3. Technological Advancements
3.1 Coating Innovations
One of the key areas of technological progress in fiberglass mesh is coating technology. Manufacturers are developing advanced coatings to enhance the performance of fiberglass mesh in different environments. For example, new generation anti-corrosion coatings are being used to protect the mesh from harsh chemicals and environmental factors, making it suitable for applications in chemical plants, wastewater treatment facilities, and coastal areas. These coatings not only improve the durability of the mesh but also extend its service life, reducing maintenance costs.
In addition, self-cleaning coatings are being explored for fiberglass mesh used in building facades and roofing applications. These coatings are designed to repel dirt, dust, and water, keeping the surface of the mesh clean and maintaining its aesthetic appeal. This innovation not only improves the appearance of buildings but also reduces the need for frequent cleaning and maintenance.
3.2 Nanocomposite Fiberglass Mesh
The integration of nanotechnology with fiberglass mesh has led to the development of nanocomposite fiberglass mesh, which offers enhanced mechanical properties and functionality. By incorporating nanoparticles such as carbon nanotubes or nanoclays into the fiberglass matrix, the resulting nanocomposite mesh exhibits improved strength, stiffness, and impact resistance.
This type of mesh is finding applications in high-stress environments, such as in the construction of bridges, high-rise buildings, and industrial structures. In the automotive industry, nanocomposite fiberglass mesh is being used to reinforce lightweight composite parts, contributing to vehicle weight reduction and improved fuel efficiency.
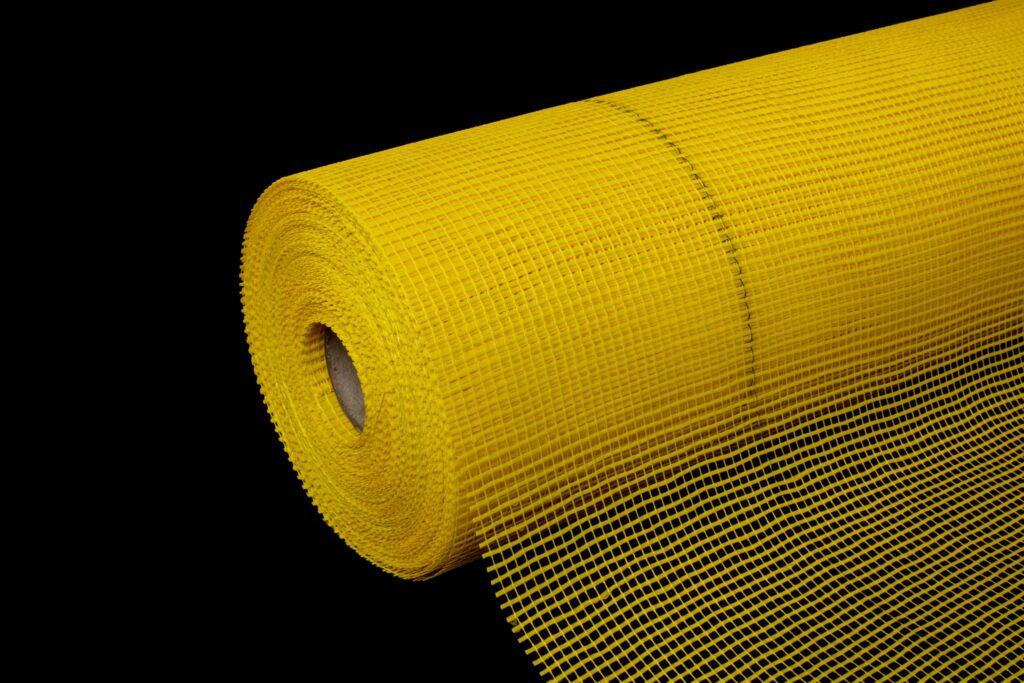
4. Key Applications
4.1.1 Wall Reinforcement
Fiberglass mesh is widely used in the construction industry for wall reinforcement. When embedded in mortar or plaster, it provides additional strength and prevents cracking due to thermal expansion, shrinkage, or mechanical stress. In masonry walls, fiberglass mesh helps to distribute loads evenly, improving the overall structural integrity of the wall.
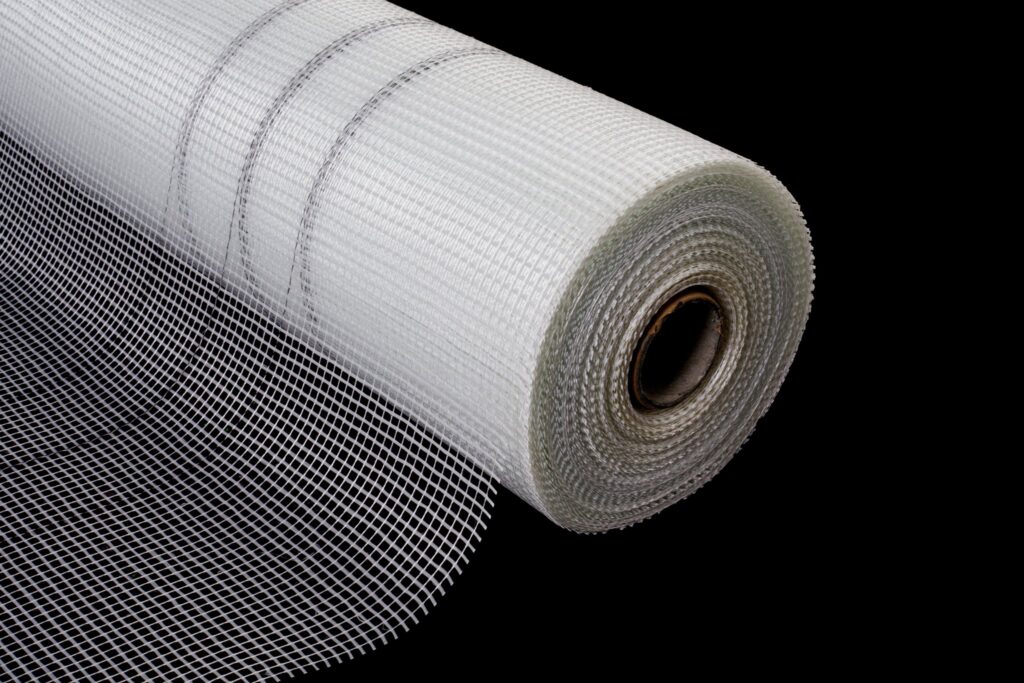
For example, in a large-scale residential construction project in [City Name], fiberglass mesh was used in the interior and exterior wall finishes. The result was a significant reduction in the occurrence of cracks, leading to a more durable and aesthetically pleasing building. The use of fiberglass mesh also simplified the construction process, as it could be easily applied and integrated with the existing construction materials.
4.1.2 Waterproofing and Thermal Insulation
In roofing and waterproofing applications, fiberglass mesh is combined with waterproof membranes to create a strong and durable waterproof barrier. It enhances the tear resistance and puncture resistance of the membrane, ensuring long-term protection against water infiltration.
In the area of thermal insulation, fiberglass mesh is used in conjunction with insulation materials such as expanded polystyrene (EPS) or extruded polystyrene (XPS) boards. It helps to bond the insulation material to the substrate and provides additional strength to the insulation system. This is particularly important in regions with extreme weather conditions, where a well-insulated building envelope is crucial for energy efficiency and occupant comfort.
4.2 Automotive and Aerospace Industries
4.2.1 Automotive Applications
In the automotive industry, fiberglass mesh is used in the production of lightweight composite parts. It is combined with resins to form strong and lightweight materials that can replace traditional metal components. For instance, fiberglass mesh-reinforced composites are used in the manufacturing of car body panels, hoods, and interior trim parts.
The use of fiberglass mesh in automotive applications offers several advantages, including weight reduction, which leads to improved fuel efficiency and reduced emissions. It also provides good corrosion resistance and design flexibility, allowing for the creation of complex shapes and structures.
4.2.2 Aerospace Applications
In the aerospace industry, fiberglass mesh plays a vital role in the construction of aircraft components. Its high strength-to-weight ratio makes it an ideal material for applications where weight reduction is critical, such as in the production of aircraft wings, fuselages, and interior components.
Fiberglass mesh-reinforced composites are also used in the manufacture of satellite structures and components. The material’s ability to withstand harsh environmental conditions, including extreme temperatures and radiation, makes it suitable for space applications. For example, in the construction of a satellite’s solar panel support structure, fiberglass mesh was used to provide the necessary strength and rigidity while keeping the weight to a minimum.
4.3 Industrial and Environmental Applications
4.3.1 Industrial Filtration
Fiberglass mesh is commonly used in industrial filtration systems to separate solids from liquids or gases. Its fine mesh structure allows for efficient filtration of particles, making it suitable for applications in industries such as food and beverage, pharmaceuticals, and chemical processing.
In a food processing plant, fiberglass mesh filters are used to remove impurities from liquids, ensuring the quality and safety of the final product. The mesh’s resistance to chemical corrosion makes it suitable for use in harsh industrial environments, where it can withstand exposure to a variety of chemicals and solvents.
4.3.2 Environmental Remediation
In environmental remediation projects, fiberglass mesh is used in applications such as soil stabilization and erosion control. When installed in the soil, it helps to reinforce the soil structure, preventing erosion and landslides. Fiberglass mesh is also used in the construction of geotextiles, which are used to separate different soil layers, filter water, and provide drainage in civil engineering projects.
For example, in a riverbank protection project, fiberglass mesh geotextiles were used to prevent soil erosion caused by water flow. The geotextiles not only stabilized the soil but also allowed for the growth of vegetation, which further enhanced the stability and ecological function of the riverbank.
6. Conclusion
The fiberglass mesh industry is witnessing significant growth and technological advancements, driven by the increasing demand for high-performance materials in various industries. With ongoing research and development efforts, new and improved fiberglass mesh products are being introduced to the market, offering enhanced properties and functionality. As industries continue to seek sustainable and cost-effective solutions, fiberglass mesh is expected to play an even more prominent role in the future, contributing to the development of innovative and efficient products and applications.