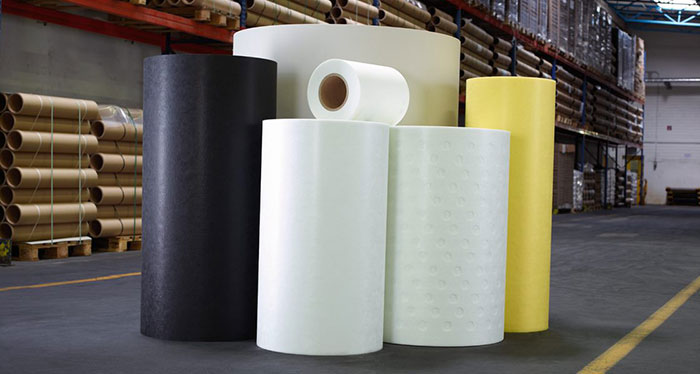
In the field of modern architectural decoration materials, LVT flooring (Luxury Vinyl Tile) has rapidly become a mainstream ground solution for residential and commercial spaces due to its excellent waterproofing, wear resistance, and diverse design styles. As the core reinforcement material of LVT flooring, fiberglass mesh plays an irreplaceable role in improving product dimensional stability, impact resistance, and service life. This article comprehensively analyzes the application value of fiberglass mesh in LVT flooring, from material characteristics and production processes to performance advantages and market trends, providing in-depth technical insights and market intelligence for foreign trade professionals and flooring industry experts.
Overview of Fiberglass Mesh and LVT Flooring
Fiberglass mesh, as a high-performance reinforcement material, has become an indispensable component in the manufacturing of modern LVT flooring (Luxury Vinyl Tile). This grid-like substrate, woven from fiberglass yarn and treated with special coatings, provides LVT flooring with exceptional dimensional stability and mechanical strength. In the multilayer structure of LVT flooring, fiberglass mesh is typically positioned between the decorative layer and the core layer, forming an invisible “skeleton” that effectively resists various stresses generated during daily use.
The manufacturing process of fiberglass mesh is highly precise.
First, glass raw materials are melted at 1600°C and drawn into continuous fibers through a specialized process. These fibers are then woven into a grid structure using a leno weave technique. To enhance its adaptability in LVT flooring environments, the mesh is further treated with polymer anti-emulsion coatings, improving its alkali resistance, flexibility, and tensile strength in both warp and weft directions. This treatment ensures strong bonding with PVC substrates while maintaining the mesh’s structural integrity.
LVT flooring, as a premium category of PVC flooring, typically consists of multiple functional layers: the top layer is a transparent wear-resistant layer providing scratch protection; beneath it is the decorative layer featuring various patterns like wood or stone grains; followed by the fiberglass mesh reinforcement layer; then the core substrate layer, usually composed of PVC, stone powder, and stabilizers; and finally the balancing layer at the bottom to counteract stresses from upper layers. In this structure, fiberglass mesh plays a critical role by not only inhibiting shrinkage and expansion but also dispersing localized impact forces to prevent cracking and deformation.
From a performance perspective, LVT flooring with fiberglass mesh exhibits multiple advantages: excellent dimensional stability with minimal deformation under temperature variations; strong impact resistance, capable of withstanding heavy object drops without damage; long service life (typically 10-15 years under normal use); as well as waterproofing, moisture resistance, flame retardancy (Class B1), and easy maintenance. These characteristics make LVT flooring particularly suitable for high-traffic commercial spaces, humid environments like kitchens and bathrooms, and facilities with high hygiene requirements such as medical and educational institutions.
As the construction industry’s demands for material performance continue to rise, the application of fiberglass mesh in LVT flooring is evolving toward higher performance and greater environmental friendliness. Some premium products now use alkali-resistant fiberglass containing zirconia, with zirconium content reaching up to 16.7%. This forms a mixed film of zirconium and titanium ions on the fiber surface, effectively resisting chemical erosion. Meanwhile, to meet green building requirements, eco-friendly fiberglass mesh with low formaldehyde and VOC emissions is gaining increasing market favor.
The Core Role of Fiberglass Mesh in LVT Flooring
As a key reinforcement material in LVT flooring structures, fiberglass mesh enhances product performance in multiple aspects through its unique physical and chemical properties. A deep understanding of these mechanisms is crucial for flooring manufacturers to optimize product design and for foreign trade professionals to accurately communicate product value.
Enhanced dimensional stability is the most notable function of fiberglass mesh in LVT flooring.
Although PVC materials offer many advantages, they exhibit significant thermal expansion and contraction under temperature variations. The high modulus of fiberglass mesh (up to 80.4 GPa) effectively suppresses these dimensional changes. Test data show that LVT flooring with fiberglass mesh exhibits a length shrinkage rate of only 0.08%-0.15% after six hours at 80°C, far lower than that of ordinary PVC flooring. This stability allows LVT flooring to be installed seamlessly over large areas without noticeable joint cracking or edge warping even in environments with large temperature fluctuations, significantly improving installation quality and service life.
In terms of mechanical performance enhancement, fiberglass mesh provides LVT flooring with exceptional tensile strength and impact resistance. Fiberglass itself has extremely high strength, and coated mesh can achieve warp and weft tensile strengths of 1,200-2,000 N/5 cm. When embedded in PVC substrates, this high-strength material markedly improves the flooring’s overall mechanical properties. Specific benefits include: resistance to heavy impacts (furniture legs are less likely to leave indentations); strong tear resistance (less damage from sharp object drops); and excellent bending resistance (reduced breakage during handling and installation). These properties make LVT flooring ideal for high-traffic venues like malls, hospitals, and schools.
Fiberglass mesh also significantly improves LVT flooring’s fatigue resistance. Traditional PVC flooring is prone to micro-cracks and structural failure under long-term alternating loads. The addition of fiberglass mesh alters stress transmission paths, effectively preventing crack propagation and extending flooring service life. Practical applications demonstrate that high-quality fiberglass mesh can increase the service life of LVT flooring by over 30% in high-intensity usage environments compared to ordinary PVC flooring. This characteristic is a key consideration for commercial clients seeking to reduce replacement frequency and long-term costs.
From a construction adaptability perspective, fiberglass mesh provides LVT flooring with superior installation performance. On one hand, the reinforcement allows for relatively thin flooring (typically 2-5 mm), simplifying height difference adjustments. On the other hand, excellent dimensional stability reduces subfloor flatness requirements, lowering leveling costs. Additionally, fiberglass mesh helps flooring better adapt to underfloor heating environments, maintaining stable performance under temperature cycling—a significant advantage for LVT flooring in northern markets.
Notably, fiberglass mesh also contributes to LVT flooring’s fire safety performance. As an incombustible material, fiberglass effectively impedes flame spread. When combined with PVC substrates, it enables LVT flooring to achieve Class B1 fire ratings (self-extinguishing when removed from flame). This feature not only meets building fire codes but also provides enhanced safety for users. In commercial projects and public facilities, fire performance is often a critical material selection criterion, and fiberglass-reinforced LVT flooring holds a clear competitive edge in this regard.
Technical Characteristics of Fiberglass Mesh and LVT Flooring Performance Optimization
The effectiveness of fiberglass mesh in LVT flooring largely depends on its technical parameters and quality levels. Understanding the relationship between these key characteristics and flooring performance helps foreign trade professionals precisely match client needs while providing manufacturers with scientific data for product formulation optimization.
Material composition is a fundamental factor influencing fiberglass mesh performance. Current mesh types for LVT flooring include medium-alkali, non-alkali, and alkali-resistant glass fibers. Non-alkali glass fibers (sodium oxide content <0.8%) offer better chemical stability and mechanical strength, making them preferable for premium LVT flooring. Alkali-resistant glass fibers incorporate zirconia (ZrO₂ content up to 16.7%) and titania to form a protective surface film, significantly enhancing chemical corrosion resistance. Although designed for cement-based environments, this alkali resistance also demonstrates excellent durability in humid LVT flooring applications. Foreign trade professionals should recommend appropriate mesh types based on regional climate and usage conditions—alkali-resistant for humid areas and more cost-effective medium-alkali for dry regions.
Physical parameters such as mesh size, weight, and thickness directly affect final flooring performance. Common mesh sizes include 3×3 mm, 4×4 mm, and 5×5 mm. Smaller meshes provide more uniform reinforcement but at higher costs. Weight (mass per unit area) typically ranges from 80-160 g/m², with higher weights indicating greater fiber content and stronger reinforcement. For example, the “160” in product code ARNP5×5-100L (160) denotes 160 g/m²—a high-specification product. Heavy-duty commercial LVT flooring should use higher-weight mesh, while residential products may opt for lighter mesh to control costs.
Mechanical properties are critical quality indicators for fiberglass mesh. Premium mesh should achieve breaking strengths of ≥1,200 N/5 cm in both warp and weft directions (as in ARNP5×5-100L). Elongation at break should remain low (~2.4%), indicating minimal deformation under stress and effective constraint of PVC substrate movement. Another key metric is modulus, with high modulus (e.g., 80.4 GPa) providing greater rigidity. When presenting to engineering-savvy clients, foreign trade professionals should emphasize these test data over generic “high-strength” claims for stronger persuasiveness.
Surface treatment processes decisively influence bonding between fiberglass mesh and PVC substrates. High-quality mesh undergoes dual treatments: first coating individual filaments with water-soluble epoxy resin and coupling agents, then applying high alkali-resistant polymer composites to the entire mesh. This ensures excellent wetting and strong adhesion with PVC resins, preventing delamination during use. Resin content (typically 12%-18%) is a crucial treatment parameter—insufficient resin weakens bonding, while excess resin may compromise flexibility and processability.
Environmental resistance is vital for assessing long-term mesh performance.
Premium mesh should exhibit: alkali resistance (≥95% alkali retention per JG158-2004), acid resistance, and water resistance. These properties ensure LVT flooring stability in humid environments and under cleaning agents. Commercial spaces frequently expose floors to chemicals, making corrosion-resistant mesh essential for preventing premature failure. When dealing with high-end clients, foreign trade professionals should proactively provide relevant chemical resistance test reports (e.g., FloorScore, DIBT certifications), as third-party endorsements significantly boost client confidence.
With diverse LVT flooring applications, special-function fiberglass meshes are emerging. Examples include conductive-fiber mesh for anti-static flooring in computer rooms and operating theaters, high-transparency mesh for decorative translucent flooring, and ultra-thin mesh (<0.1 mm) for slim LVT (1.5-2 mm). Knowledge of these specialty meshes helps foreign trade professionals tap niche markets and offer differentiated products.
Production Processes and Quality Control of Fiberglass Mesh in LVT Flooring
Integrating fiberglass mesh into LVT flooring requires precise process control and strict quality management. This stage directly determines final product performance and consistency—it represents core technology for manufacturers and showcases corporate strength for foreign trade professionals.
In LVT flooring production, fiberglass mesh lamination typically occurs during calendering or extrusion. In standard dry processes, PVC resin powder, stone powder, plasticizers, and stabilizers are first mixed into dry blends, then formed into substrate layers via extruders. Pre-spread fiberglass mesh is accurately fed into molten PVC to form a sandwich structure—PVC layers above and below with mesh reinforcement in between. Temperature control is critical here (typically 180-200°C) to ensure PVC fully melts and bonds with mesh without damaging fibers. Pressure (10-15 MPa) affects impregnation quality, ensuring PVC completely penetrates mesh openings.
Mesh pretreatment ensures good bonding. While quality fiberglass mesh undergoes coupling agent treatment during manufacturing, some producers apply secondary activation (e.g., plasma or chemical priming) to further improve PVC affinity. Treated mesh must maintain proper moisture content (<0.1%)—excess moisture causes bubbles and bonding defects during high-temperature processing. When evaluating suppliers, foreign trade professionals should examine mesh pretreatment processes as indicators of product tier differentiation.
Lamination process precision impacts LVT flooring structural integrity. Multilayer materials (wear layer, decorative layer, fiberglass mesh, core layer, and balancing layer) require exact hot-press lamination. Modern lines use continuous roller systems with zoned temperature control: initial high temperatures (190-210°C) ensure layer fusion, followed by gradual cooling (120-150°C) for shaping and stress reduction. Fiberglass mesh must maintain uniform tension throughout—looseness causes wrinkles while over-tensioning may deform or break fibers. Advanced equipment employs laser alignment and automatic tension control to maintain optimal mesh conditions.
Curing treatment is an easily overlooked yet vital production step. Fiberglass-reinforced LVT flooring requires 24-48 hours of controlled curing (typically 23±2°C, 50±5% RH) post-lamination. This allows internal stress release and stabilizes PVC-fiberglass bonding. Inadequate curing leads to subsequent warping or cracking. Large manufacturers maintain dedicated curing rooms, while some small factories shorten curing times to accelerate delivery—a key quality control point foreign trade professionals should note when assessing suppliers.
Quality inspection systems ensure batch consistency and reliability. Key tests for fiberglass mesh reinforcement include: peel strength (evaluating mesh-PVC bonding), dimensional stability (shrinkage after six hours at 80°C), anti-warping tests, and long-term thermal cycling tests. International leaders like Saint-Gobain enforce stricter corporate standards (e.g., requiring <1.2 mm heat warping versus industry-standard 2 mm). When targeting quality-conscious clients (e.g., European buyers), foreign trade professionals should highlight these superior quality measures as key competitive advantages.
Defect analysis expertise helps foreign trade professionals better address complaints and propose solutions. Common fiberglass mesh-related LVT flooring issues include: delamination (mesh-PVC separation), wrinkling (uneven mesh laying), deformation (uneven mesh stress or insufficient curing), and white edges (exposed fibers during cutting). Most stem from improper material selection or poor process control. For example, low-resin cheap mesh often causes delamination, while insufficient curing typically manifests as edge warping post-installation. Foreign trade professionals with this knowledge can handle client feedback more professionally and guide factories in targeted improvements.
With smart manufacturing advancements, fiberglass mesh application in LVT flooring is becoming increasingly precise. Leading manufacturers now employ computer vision for real-time mesh positioning monitoring, big data for process optimization, and AI algorithms for defect prediction and prevention. These technologies improve product consistency, reduce waste, and enhance premium LVT production efficiency. When promoting products, foreign trade professionals can showcase factory smart capabilities to strengthen client confidence in quality and supply reliability—particularly when dealing with innovation-focused multinational buyers.